Mit der Kanban-Methode Lagerbestände messen und steuern
Die Kanban-Methode ermöglich auf effiziente Weise, den Lagerbestand zu messen und steuern. Für Produzenten, Logistiker und Händler ist dies essenziell.
Wie diese Methode der Lagerverwaltung funktioniert und wie man sie als Unternehmer für sich nutzen kann, erläutert dieser Artikel.
Welche Bedeutung hat der Lagerbestand?
Produzenten und Händler lagern ihre Waren und müssen diesen Bestand kontrollieren. Dies ist wichtig für die zeitnahe Belieferung der Kunden. Lagerkapazitäten kosten jedoch Geld, weshalb es gilt, das Lager stets optimal auszulasten. Ein zu großes Lager wäre zu teuer, ein zu kleines Lager würde an Kapazitätsgrenzen stoßen. Das optimal dimensionierte Lager soll stets einen Bestand aufweisen, der die jederzeitige Belieferung der Abnehmer nach Bedarf und/oder Plan ermöglicht. Es kann und darf aber nicht überfüllt werden. Daher ist eine Kontrolle und Steuerung des Lagerbestands unerlässlich. Nur so lassen sich stabile Lieferanten-Kunden-Beziehungen zu vertretbaren Kosten etablieren. Die Kanban-Methode dient der Kontrolle und Steuerung des Lagerbestands.
Optimierung der Lagerverwaltung
Lagerbestände sind eine Möglichkeit, den Kunden auch bei verzögerter Produktion oder ausgefallenen Lieferketten zu beliefern. Die pünktliche Lieferung hat oberste Priorität, doch sie darf nicht durch ein sehr großes Lager zu teuer werden. Ideal sind relativ niedrige Lagerbestände, die stets das fristgerechte Beliefern absichern, aber auch Kapazitäten für Nachschub aus der Produktion freihalten. Es gilt vom Grundsatz her: Das Lager soll so voll wie nötig, aber so leer wie möglich sein. Die Anwendung der Kanban-Methode realisiert dieses Ziel.
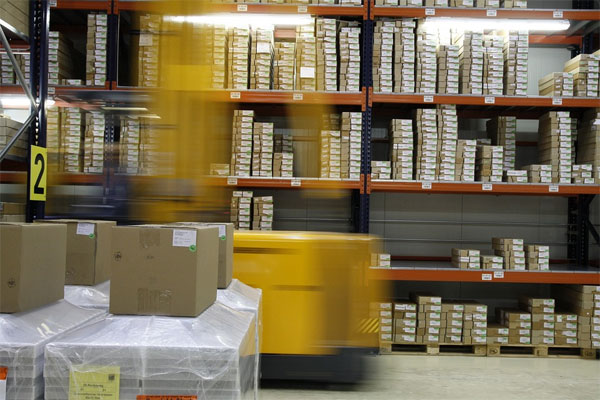
Lagerbestand | Foto: delphinmedia, pixabay.com, Pixabay License
Wie funktioniert die Kaban-Methode?
Mit der Kanban-Methode verbessert sich die Lagerverwaltung auf dem exakt erforderlichen Niveau. Kanban funktioniert rein technisch denkbar einfach: Auf einer Karte oder einem Blatt Papier bei jeder Charge des Lagerguts sind drei wesentliche Informationen vermerkt:
- #1 Informationen zur Identifikation: Teilenummer, Stückzahl pro Behälter, gegebenenfalls Foto des Teils
- #2 Informationen zum Tracking: Kunden- und Lieferantenidentifikation, Abstellort des Behälters, Ablageort für freigegebene Kanban-Karten
- #3 Informationen zum Management: Zahl der umlaufenden Kanban-Karten, Anfangsgröße der Charge (Referenz für die Überprüfung der implementierten Kanban-Schleife)
Als Kanban-Schleife wird der Kreislauf der Kanban-Karten bezeichnet. Bei einer gegebenen Referenzgröße genügt ein Kanban-Kartensatz pro Teilevariante. Wenn er einmal umgelaufen ist, wurde der Kunde vollständig beliefert, die nächste Teilelieferung liegt im Lager. Die kontinuierliche Belieferung erfolgt auf Pull-Basis, bei welcher der Kunde die Downstreamposition einnimmt und upstream die Produktion (und damit die Lagerbefüllung) steuert. Kanban kann allerdings auf zwei Arten stattfinden: als Produktions- sowie als Transfer- oder Auslieferungskanban. Beim Produktionskanban beeinflusst die Kanban-Schleife den Rhythmus der Produktion, beim Transfer- oder Auslieferungskanban die Befüllung des Lagers ab Werk und die Auslieferung an den Kunden, somit also auch die Dauer der Lagerhaltung.
Fazit: Wie effizient ist die Kaban Methode?
Mit der Kanban-Methode ist das Lager immer optimal gefüllt. Der Kunde kann stets beliefert werden. Die Voraussetzung hierfür ist, dass die Produktion reibungslos läuft, es also keine Engpässe bei Nachlieferungen an das Lager gibt.